Case Study: Producing Animal Bedding from Miscanthus
BACKGROUND
Burlerrow Farm is a 303-hectare mixed farm based in Bodmin, Cornwall. It is run by James Mutton who has been growing miscanthus since 2002. Initially, the crop was used to produce miscanthus rhizomes, but since 2009 they have been producing premium equine and animal bedding. In 2022, the farm business processed over 4,000 tonnes of miscanthus for this purpose. During the last decade Burlerrow Farm has diversified into new markets and now produce miscanthus bedding products (Burlybed), heating briquettes (Burlyburn), and forage products (Burlybale) based on grass, hay or haylage.
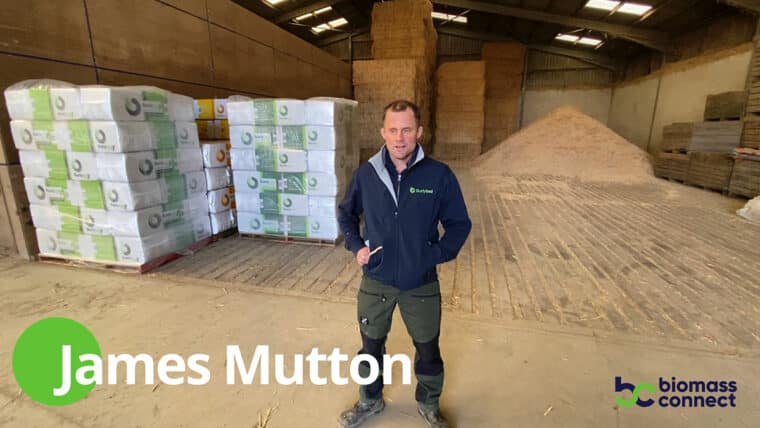
Burlybed Products
Products are sold through 100 retailers across the south of England and Wales with the furthest north in Worcestershire and east to Bedfordshire, Essex and Kent.
The farm has agreements in place with 20 miscanthus growers. Eleven of these are based in Cornwall and Devon with Burlerrow Farm contracted to manage the crop. A further nine growers are in Herefordshire, Berkshire, and Somerset. In these cases, the grower manages the crop and sells the bales to Burlerrow Farm.
The Burlerrow Farm premises are heated with an Eta Hack 90 kW biomass boiler fuelled with miscanthus chips. The farm also supplies a separate family-owned district heating scheme (Coldrenick Farm Offices) 5 miles away. The latter has a 130 kW Eta Hack boiler and heats five offices and a farmhouse.
Business Objectives
James Mutton started growing miscanthus as a rhizome producer for Bical in 2003. This contract ceased in 2008 when Bical went out of business. Mr Mutton began exploring the animal bedding market in 2009 and early trials of a basic specification were a success with favourable feedback from local users (keepers of horses, dairy/beef cattle, poultry and pets).
Mr Mutton was one of the first farmers to benefit from funding under the England Rural Development Programme. This provided a 40% grant towards the £400,000 capital costs of a miscanthus processing facility. The facility includes a 1,100 square metre storage shed, dust extraction equipment, bagging plant and briquetting press. A drying floor was added later at a cost of £50,000.
In 2017, the farm was successful in a bid for a £35,000 LEADER grant. This was secured through the
Atlantic and Moor Local Action Group and enabled the farm to add a shredding system into the processing line.
The family business invested in two biomass boilers in 2011 and 2012. These were accredited under the Renewable Heat Incentive (RHI). In total, the two boilers require around 100 tonnes of miscanthus chip per year.
Business Successes
The business has grown in capacity over the last decade. In 2011, the operation processed around 2,000 tonnes of bedding doubling to 4,000 tonnes in 2022.
Currently the farm produces approximately 600 tonnes of miscanthus per year from their own fields (50 hectares) and buys the rest (3,700 tonnes) from 20 growers.
A key to success was focusing on producing a premium product. Mr Mutton realized the qualities of miscanthus over alternative bedding materials, and the potential to highlight its traceability and sustainability compared to alternatives. This made equine bedding an ideal market.
In 2022, Burlerrow farm produced 170,000 premium grade equine bales. Each bale weighs 19kg and retails [in 2023] for £8-£10 per bale. The quality of miscanthus horse bedding products has been ranked highly alongside other types of premium horse bedding brands in the UK1.
Miscanthus horse bedding is particularly interesting to stables as it has a spongy inner core that absorbs up to three times its own weight in moisture and reduces the smell of urine and faeces. As a result, it doesn’t need to be replaced as often.
A typical horse owner would need to start with 5-7 bales topping up with 1-2 bales a week. This equates to 70-80 bales a year costing around £600-£650.
During the processing of equine bedding 20% of the miscanthus is removed as fines. This can be used to produce briquettes and pellets. In 2022, 800 tonnes was processed in this form (200 tonnes of briquettes and 600 of pellets).
Burlyburn briquettes are sold in 15kg bags for £6.50 each in local garage forecourts and by around 25 of the retailers that also sell bedding. They burn well and have a high calorific value but do have a higher ash content than wood briquettes.
The pellets produced are not fuel pellet grade (due to durability and ash content) and are used mainly for bedding. Users need to break them up and sprinkle with water to create a fluffy bed.
Burlyburn also produce a range of firelighters. These are produced by another supplier and include miscanthus mixed with recycled candle wax. Burlerrow Farm sells around 4,000 boxes per year. Although, the profit margin is minimal, the firelighters promote the briquettes and help with the communication of a positive story involving a circular economy of biobased materials.
Through the management of other growers’ land, Burlerrow Farm have improved the husbandry of the crop and increased yields. New activities include post-harvest management such as sub-soiling every 3-4 years to rejuvenate the rhizomes and deal with compaction, soil analysis every 3-4 years to enable intervention where necessary (e.g. supplements to adjust pH and concentrations of trace elements) and better weed control.
Challenges
The expansion of the Burlybed brand was dealt a blow in 2019 when there was a major fire in the barn and storage area. The facilities were replaced in full, but this caused a great deal of upheaval for the best part of a year.
However, the main issue with increasing production is the limited availability of miscanthus. Burlerrow Farm are looking to source 5,000 tonnes in 2023 but this is proving difficult.
Burlerrow Farm doesn’t have a contract with their growers. Although, the farm would like a greater degree of clarity to shore up supply, the message they get from their growers is that they don’t want to be tied into a long-term deal.
Burlybed are hoping to expand beyond the south of England and Wales into the Midlands (Nottinghamshire, Leicestershire and Derbyshire). However, this is not easy as their main competitor (Ethos) is located in the Midlands which means they can achieve much lower haulage costs.
By being very early adopters of biomass boiler technology, the farm is exempt from RHI air quality emission thresholds. This came into force in September 2013 and required boilers to have emissions certificates for particulates and nitrogen oxides. Mr Mutton is one of several growers in the SW using miscanthus in an Eta boiler and has found that it works well with this fuel.
Other growers could follow the Burlerrow Farm example, but they would be required to perform an in-situ emissions test, which is expensive and install additional abatement equipment. As a result, on-farm use of miscanthus in biomass boilers has not been widely replicated.
Cost and benefits
In 2022 Burlerrow Farm were offering growers £74/tonne ex farm for miscanthus bales. This is a competitive price compared to other end markets for miscanthus cane. A farmer achieving a 12 tonne per hectare yield should therefore be able to achieve a net return of ~£400 per hectare per year.
Mr Mutton achieves yields of around 12 tonnes per hectare (@ 15% moisture content) on his own land. The only ongoing cost is chip harvesting each year. This would mean an annualised production cost of around 1.1 pence per kWh when used in his boiler.
On top of this, other costs should be included such as lost income from the land (£200 per year), costs associated with RHI compliance (e.g. Sustainable Fuel Register fees of £200 per year) and additional servicing and parts for the boiler (£300 per year). Even with these costs, the price of self-supply miscanthus is only 2.75p/kWh which is a huge saving on the alternative of purchased woodchip (currently around 4.8p/kWh) or oil / gas (currently over 10p/kWh).
Mr Mutton’s first miscanthus crops will be harvested for the 20th time this year. The yields being achieved do not suggest any falling off in viability and the plantations may last longer than 25 years. So, based on annualized costs of establishment, the miscanthus production price is likely to fall.
In 2020, Mr Mutton entered into a Countryside Stewardship agreement. This includes a wide wildlife margin around the outside of the miscanthus crop. This is worth £250 per hectare of nonplanted area and will help to further increase the farm’s enterprise margins.
Burlerrow Farm currently employs 8 people to process and market the Burlybed, Burlyburn and Burlybale range.
- Miscanthus Crop
- Miscanthus Bales
Lessons Learnt and Recommendations
Mr Mutton and his family have fully embraced the opportunity to develop a business from miscanthus. It has been a huge learning curve, but Mr Mutton has remained open to new ideas and market opportunities. He has also been very adept at gaining funding for these enterprises and as a result has created a thriving business.
The Burlerrow Farm team are always looking to innovate and increase efficiency. For instance, the farm is currently developing a pelleting process where fines (<3mm particles) removed during processing are immediately turned into pellets without unnecessary movement or storage of the powdery material.
This is an efficiency saving but also reduces airborne particles, improving working conditions for his employees.
Efficiency savings are also being made in the miscanthus crop. Mr Mutton is starting to rake leaf and stubble in the crop every 3-4 years. This doesn’t impact on the potential productivity of the crop and increases the harvested biomass by 25% in the years that it is done. This material is suitable for making fuel logs and pellets.
The team are also looking at energy saving operations, with solar PV due to be installed on the roofs of production buildings and a ground mounted system being investigated to increase the business’ self-sufficiency.
1 Choosing the right bedding for you and your horse
Horse and Hound, 31 July 2021